Continuous Improvement Drives Operational Success
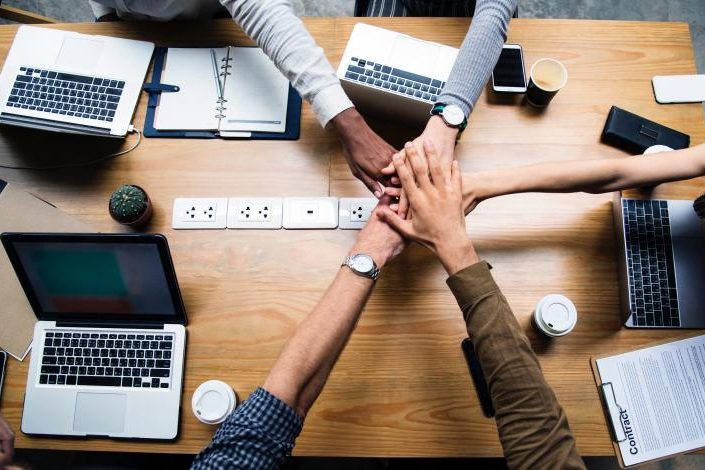
Leadership mindset shapes the direction of an organization and is reflected in how an organization handles change. How can you positively support your company to manage and optimize so that change means ongoing operational improvement instead of chaos? A culture of Continuous Improvement is key in many business areas, operations included.
The Continuous Improvement process begins by evaluating, at the site-level, where the organization is today. From here, identified areas of opportunity are addressed through strategic and tactical next steps at each cascading organizational level. Unified understanding and strong communication is essential to simplify processes. This allows for fewer touches, reduced costs, and quicker delivery. To foster this, the right management system needs to be implemented with a dedicated team of Continuous Improvement professionals supported by a framework developed using three Continuous Improvement concepts: 5S, Standard Work, and Visual Management.
5S
5S is a term for a workplace methodology that describes how to organize a work space efficiently and effectively using a list of five Japanese word: seiri (“Sort”), seiton (“Set in Order”), seiso (“Shine), seiketsu (“Standardize”) and shitsuke (“Sustain”). These five words describe how to identify and store items used, how to maintain the area and items, and how to sustain the new order created.
To set up the workspace, first apply seiri and seiton. Begin by sorting through all items in a location and removing what is unnecessary to reduce time loss, simplify inspection, and increase amount of available space. Then, place the necessary items in their optimal place to fulfill their function to enable a smooth and easy workplace flow. Once the workspace is set up, maintain through seiso by regularly cleaning and inspecting to prevent deterioration and keep the workplace safe. The first three steps are then standardized into a routine process to develop a work structure sustained by self-disciplined implementation.
The implementation of the 5S methodology can significantly transform a facility, such as streamlining Return to Vendor processes by replacing a common open area of varied pallets for multiple vendors with clearly marked vendor-specific lanes.
Standard Work
Standard Work breaks down processes into sequenced and organized pieces with specific work instructions ensures delivery on consistency, timeliness, and repeatability. Each step is well-defined and these detailed work instructions can be kept in a centralized database. Used in conjunction with leaders trained in Continuous Improvement, these creates predictability and efficiency across locations with minimal variance in quality of work and output. However, the concept of Standard Work extends past standardizing a process. The process developed to perform a task should always be the most efficient known method, meaning that it is a team effort to continuously improve the standard and share new best practices.
Visual Management
Successful implementation of a developed strategy requires effective performance management with clear communication of expectations and progress. Visual Management is a technique that uses visual signals in place of text to convey messages more quickly and effectively. When used well, Visual Management enables teams to easily share information with each other, enforce standards, bring attention to irregularities, react productively to irregularities, and put measures in place to prevent future reoccurrences of irregularities. Visual Management provides the accessibility to performance feedback needed to engage employees quickly in the areas of opportunity.
Common examples of Visual Management in daily life include stoplights to manage traffic flow and low battery icons to indicate irregularity. In an operations facility, this can look like flags on Pick-to-Light (PTL) carts so that pickers can identify which cart they need and manage flow to know which carts are available. Visual Management could also take the form of hourly performance dashboards used to guide team huddles by identifying irregularities in the process for immediate improvement. Simplicity is key in developing Visual Management boards, with the focus on vital measurements displayed consistently.
Lead with the mindset of striving to be a little better than yesterday, embracing change and continuously improving. At Radial, we have seen the implementation of Continuous Improvement concepts significantly improve our operations and are ready to partner with you to help you get your company to the next level.