Fulfillment Centers: The Powerhouse Behind Seamless eCommerce
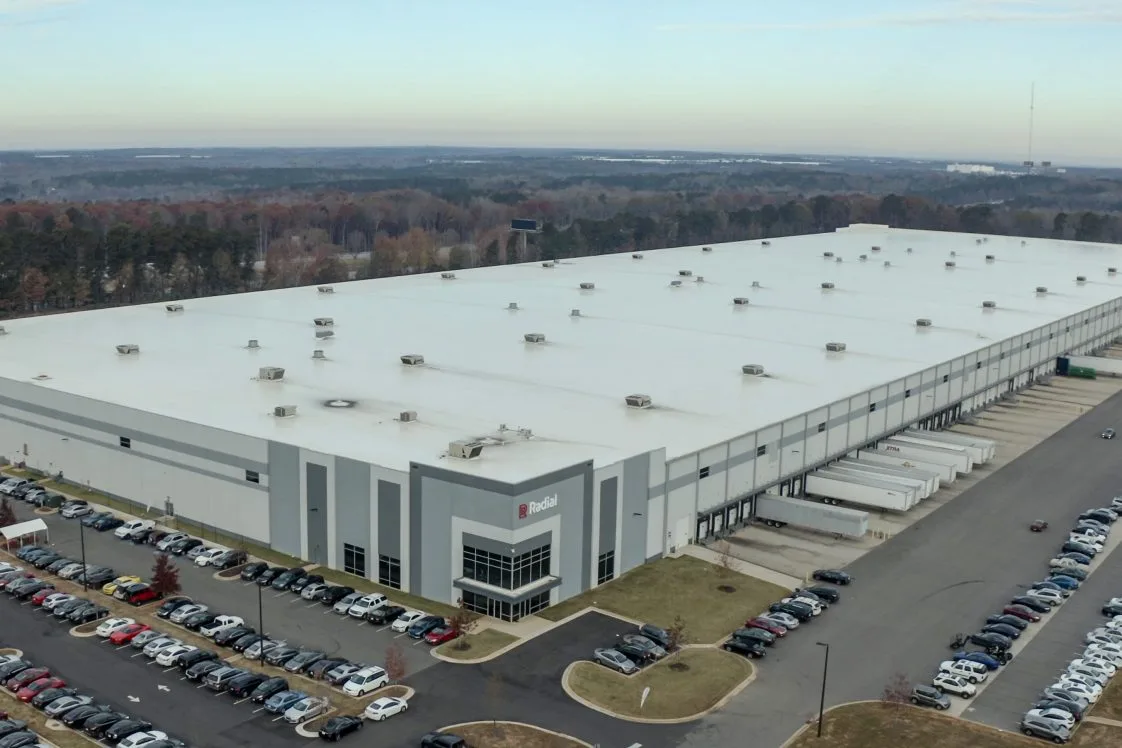
Fulfillment centers play a critical role in ensuring seamless order fulfillment and customer satisfaction. They serve as the backbone for eCommerce retailers, managing the complex processes required to receive, process, and deliver customer orders. Fulfillment centers execute everything from order management, inventory management, warehousing, picking and packing, and shipping and returns.
Let’s explore the inner workings of fulfillment centers and how they can drive seamless eCommerce operations.
What is a Fulfillment Center?
A fulfillment center is a specialized facility or warehouse where third-party logistics (3PL) and eCommerce companies store, process, and fulfill customer orders for their products. It serves as a central hub for order fulfillment so that businesses efficiently manage their inventories and ensure timely and accurate delivery to customers.
The primary functions of a fulfillment center include receiving and storing inventory, processing customer orders, picking and packing items, conducting quality control checks, and coordinating shipping and delivery. These centers are designed to handle large order volumes and often employ advanced technologies and automation systems to streamline operations and improve efficiency.
Fulfillment centers are a critical part of the eCommerce ecosystem, especially for retailers who don’t have the infrastructure to handle order fulfillment in-house. Instead, they work with third-party fulfillment partners who provide eCommerce fulfillment solutions. They enable businesses to outsource order fulfillment and focus on core activities like product development, marketing, and customer engagement. By working with 3PLs, companies can benefit from economies of scale, reduce operational costs, and offer faster shipping times to customers.
Fulfillment Centers Versus Warehouses
Fulfillment centers differ from warehouses in the types of services they offer and how they function. Warehouses are primarily designed and used for storing and managing inventory. Fulfillment centers are designed to incorporate eCommerce order processing, inventory management, and transportation. Fulfillment centers have to operate with greater complexity than warehouses. For example, fulfillment centers typically have real-time inventory management and handle more customer-facing operations, while warehouses don’t typically have the same capabilities and don’t directly interact with customers.
The Role of Fulfillment Centers in Supply Chains
Fulfillment centers play a pivotal role in retailers’ supply chains. They are the intermediaries between businesses and customers and serve as the locus of customer-facing activities like order fulfillment and delivery. Their key functions include:
- Order processing and management
- Inventory storage and management
- Pick and pack operations
- Quality control and packaging
- Shipping and logistics
By performing these functions, fulfillment centers streamline the order fulfillment process, reduce processing time, improve order accuracy, and enhance overall customer satisfaction. They play a critical role in the delivery of products from the point of sale to the customer’s doorstep.
Order Processing and Management
When a customer places an order online, fulfillment centers receive the order and process it. They will verify order details, check product availability, and ensure accurate order processing, including order confirmation, package tracking, and managing changes or cancellations.
Inventory Storage and Management
Fulfillment centers serve as storage hubs for eCommerce inventory. They manage stock levels, track inventory movement, and ensure efficient product organization and storage. Operations can employ real-time inventory management systems to monitor stock availability and facilitate timely replenishment.
Pick and Pack Operations
Team members pick and pack online orders in fulfillment centers. They gather the products according to order specifications, verify order details, and package them appropriately for shipment. Fulfillment centers leverage different picking strategies, like batch picking or zone picking to maximize efficiency.
Quality Control and Packaging
Fulfillment centers conduct quality control checks to ensure the accuracy, condition, and completeness of ordered items. They inspect products for defects, verify proper labeling, and ensure that the packaging meets shipping standards for transit. Quality control measures mean customers are satisfied with their deliveries and are less likely to return or exchange items.
Shipping and Logistics
Once the items are picked, packed, and quality checked, fulfillment centers ship and monitor order delivery. They partner with shipping carriers, arrange transportation, and select appropriate shipping methods to ensure on-time delivery. eCommerce retailers know that timely delivery is key to meeting high customer expectations. Twenty-nine percent of customers abandon online orders over slow shipping.
The Advantages of Using Fulfillment Centers
Businesses benefit when they leverage fulfillment centers. Retailers can streamline operations, focus on core competencies, and provide exceptional customer experiences. Fulfillment centers help businesses scale effectively, minimize costs, and deliver products to customers quickly and accurately.
Improved Efficiency and Order Accuracy
Fulfillment centers are designed to fulfill online orders efficiently and accurately, employing streamlined operations and advanced technologies to optimize eCommerce logistics. Experienced teams understand how to handle large order volumes, reduce errors, and improve overall efficiency.
Faster Order Processing and Fulfillment
With dedicated resources and efficient workflows, fulfillment centers expedite order processing and fulfillment. They have streamlined processes, advanced inventory management systems, and optimized pick and pack operations. The result: shorter order fulfillment cycles and faster delivery to customers.
Cost Savings and Economies of Scale
Fulfillment centers can provide cost savings through economies of scale. They handle a high volume of orders, allowing businesses to benefit from bulk shipping rates, reduced packaging costs, and optimized warehouse space. By outsourcing order fulfillment, eCommerce stores can avoid investing in their own warehouse facilities and associated operational expenses. That means scalable logistics solutions that save eCommerce merchants money and improve customer experiences.
Scalability and Flexibility for Business Growth
Fulfillment centers offer scalability and flexibility to accommodate fluctuations in demand and support retailer growth. They have the infrastructure, resources, and expertise to handle fluctuations in order volumes, seasonal demands, and expansion into new markets. Fulfillment centers can quickly adapt to changing business needs, ensuring seamless order fulfillment during periods of both increased and decreased consumer demand.
Enhanced Customer Experience and Satisfaction:
Seventy-nine percent of consumers report that they may not purchase again from a brand after a poor post-purchase experience. Efficient order processing, faster shipping times, accurate order fulfillment, and reliable tracking systems create better customer experiences and build long-term loyalty. Fulfillment centers meet customer expectations by providing timely deliveries and handling returns or exchanges efficiently. This results in higher customer satisfaction, improved brand reputation, and increased customer loyalty.
Key Technologies and Automation in Fulfillment Centers
Fulfillment centers leverage various technologies and automations to optimize their operations. These technologies help fulfillment centers operate with greater speed, accuracy, and efficiency. They minimize human errors, optimize inventory management, and provide real-time visibility into operations. By leveraging these key technologies, fulfillment centers can effectively handle high order volumes, meet customer expectations, and deliver seamless order fulfillment.
Warehouse Management Systems (WMS)
Warehouse Management Systems (WMS) are software applications specifically designed to manage and control the day-to-day operations of a warehouse or fulfillment center. WMS tracks inventory, manages picking and packing processes, optimizes storage, and provides real-time visibility into operations. It streamlines workflows, enhances inventory accuracy, and improves overall efficiency.
Robotics and Automation
Fulfillment centers employ robotics and automation technologies to enhance efficiency and speed in various processes. Automated guided vehicles (AGVs) and robotic arms assist in material handling and picking tasks. Automated conveyor systems and sorting machines facilitate the movement of packages, while automated storage and retrieval systems (AS/RS) optimize space utilization and retrieval processes.
Inventory Tracking and Management Software
Fulfillment centers use inventory tracking and management software to monitor and control inventory levels in real time. It tracks product movement, provides visibility into stock levels, automates stock replenishment, and assists in demand forecasting. Per Gartner, 51% of surveyed organizations switch to inventory management software to reduce inefficiencies with existing tools and processes. Inventory management technology helps optimize inventory accuracy, minimize stockouts, and improve order fulfillment efficiency.
Barcoding and Scanning Technology
Fulfillment centers use barcoding and scanning technology in the pick and pack process. Each product is assigned a unique barcode, which is scanned during various stages of fulfillment. Scanners capture item information, verify accuracy, update inventory records, and facilitate order tracking.
Integration with eCommerce Platforms and Order Management Systems
Fulfillment centers integrate with eCommerce platforms, like Shopify, and order management systems to streamline the flow of information. The integration allows for seamless transfer of order data, inventory updates, and tracking information. That means fulfillment centers have real-time access to order details for efficient order processing, inventory management, and synchronization with customer-facing platforms.
Fulfillment Center Best Practices for Small Businesses
High performance requires regular evaluation, continuous improvement, and adaptation to changing business needs. Now that we have covered how fulfillment centers work in detail, let’s dive into best practices to optimize operations, reduce errors, and improve customer satisfaction.
Efficient Warehouse Layout and Organization
Designing an efficient warehouse layout minimizes travel time and improves productivity. Grouping products logically, optimizing storage space, and implementing clear aisle markings contribute to efficient movement within the facility. The layout should consider factors such as product popularity, order frequency, order picking paths, and relevant picking processes.
Accurate Inventory Management and Real-time Tracking
Accurate inventory management is crucial to avoid stockouts or overstock situations. Utilizing inventory management systems and real-time tracking technologies enables fulfillment centers to maintain accurate inventory counts, monitor stock levels, and facilitate timely replenishment. This minimizes delays, improves order fulfillment accuracy, and enhances customer satisfaction.
Streamlined Pick and Pack Processes
Streamlining pick and pack processes reduces order processing time and increases efficiency. Implementing batch picking or zone picking strategies, optimizing picking routes, and employing technology like barcode scanning can expedite order fulfillment. Additionally, utilizing order batching and sorting techniques post-picking can further streamline the packing process.
Quality Control Measures and Packaging Standards
Implementing stringent quality control measures ensures accurate order fulfillment and minimizes errors. Regular inspections of picked items, adherence to packaging standards, and thorough quality checks reduce the chances of shipping incorrect or damaged products. High-quality packaging materials and proper labeling contribute to product protection, customer satisfaction, and can even reduce costs in some instances.
Collaboration with Shipping and Logistics Partners
Establishing strong relationships and clear communication channels with shipping carriers and logistics providers helps streamline shipping processes, optimize delivery routes, and provide reliable tracking information. Effective collaboration ensures on-time deliveries and fulfilled delivery promises.
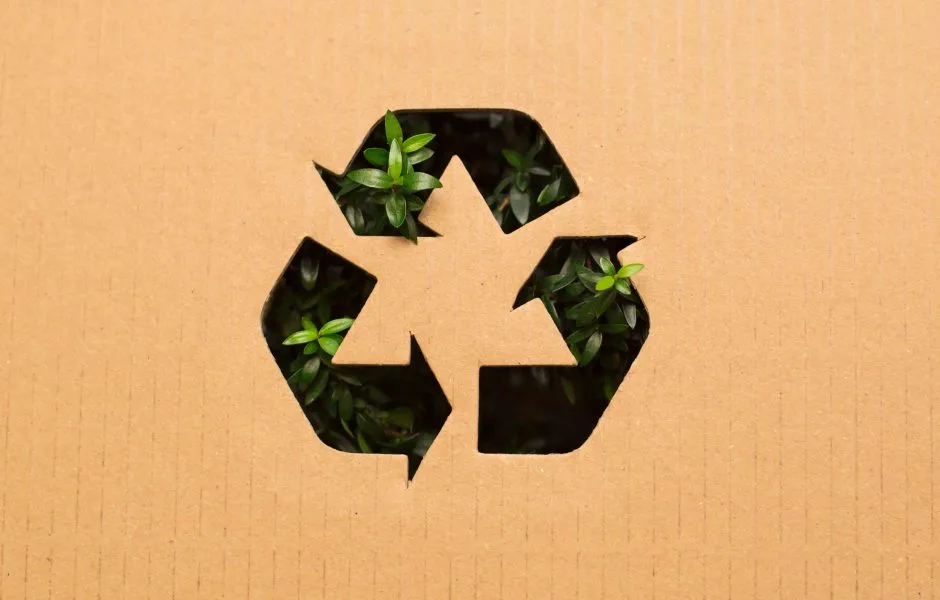
Future Trends and Challenges in Fulfillment Centers
The future of fulfillment centers will be shaped by the adoption of emerging technologies, a focus on sustainability, addressing workforce challenges, ensuring data security, and embracing continuous improvement to meet the evolving demands of customers
- Increased Adoption of Robotics and Automation: Fulfillment centers will continue to adopt advanced robotics and automation technologies. Robots can handle tasks like picking, packing, and sorting, reducing manual labor and increasing productivity. However, integrating these technologies seamlessly and addressing potential job displacement concerns will be challenging.
- Expansion of Omnichannel Fulfillment: With the rise of eCommerce and customer expectations for fast and flexible delivery options, fulfillment centers will need to adapt to an omnichannel approach. This means fulfilling orders from multiple channels (online, mobile, brick-and-mortar) while maintaining inventory accuracy and optimizing order routing to minimize costs.
- Demand for Same-Day and Last-Mile Delivery: Customers increasingly expect faster delivery times, including same-day and last-mile delivery options. Fulfillment centers will need to optimize their processes to fulfill orders more quickly and efficiently, relying on technologies like route optimization, autonomous vehicles, and drones.
- Focus on Sustainability and Eco-Friendly Practices: Environmental sustainability will play a significant role in the future of fulfillment centers. Companies will need to adopt eco-friendly practices across supply chains, such as using renewable energy sources, optimizing packaging to reduce waste, implementing recycling programs, and reducing carbon emissions from transportation.
- Integration of Artificial Intelligence and Machine Learning: Artificial intelligence (AI) and machine learning (ML) algorithms will be used increasingly in fulfillment centers to optimize operations. AI can be utilized for demand forecasting, inventory management, route optimization, and quality control, leading to improved efficiency and cost savings.
- Advanced Data Analytics for Operational Insights: Fulfillment centers will leverage advanced data analytics to gain actionable insights into their operations. By analyzing data related to inventory, order fulfillment, customer behavior, and operational efficiency, companies can identify areas for improvement, make data-driven decisions, and enhance overall performance.
- Workforce Challenges and Labor Management: Fulfillment centers will face challenges managing a diverse workforce, including temporary and seasonal workers. Fulfillment centers will need to address issues such as training, workforce planning, employee engagement, and retention to ensure smooth operations and meet customer demands.
- Data Security and Privacy: Operators will need to ensure data security and privacy as fulfillment operations increasingly rely on technology and data to operate. Companies must implement robust cybersecurity measures, encryption protocols, and access controls to protect sensitive customer information and prevent data breaches.
- Continuous Process Improvement: Fulfillment centers will need to embrace a culture of continuous process improvement to stay competitive. Regularly evaluating and optimizing workflows, implementing lean practices, and leveraging technology advancements will be essential to drive efficiency and customer satisfaction.
- Regulatory Compliance: Fulfillment centers will need to navigate and comply with evolving regulations, both domestically and internationally, such as safety standards, labor laws, and customs requirements. Staying up to date with changing regulations and implementing necessary measures will be critical to avoid penalties and maintain smooth operations.
The Future of Fulfillment Centers in the Ever-Changing eCommerce Landscape
Fulfillment centers are poised to undergo significant transformations to meet the evolving demands of customers and businesses. Emerging technologies like automation, robotics, AI, and IoT will revolutionize fulfillment operations, enabling higher efficiency, accuracy, and speed. The integration of physical and digital commerce will become essential as the distinction between online and offline retail continues to blur.
As fulfillment centers adapt to the ever-changing commerce landscape, they will play a role in shaping the future of retail and customer experience. By embracing emerging technologies, sustainable practices, workforce management strategies, and data security measures, fulfillment centers will drive seamless, efficient, and customer-centric commerce.
Unlock the full potential of your eCommerce business with Radial, a leading 3PL provider. Radial streamlines order fulfillment with 30+ years of experience and cutting-edge solutions. With our unmatched expertise, scalable infrastructure, and innovative technology, we ensure your orders are processed accurately and efficiently, from inventory management to pick and pack operations and timely delivery. Our global network empowers you to expand your reach and deliver exceptional customer experiences worldwide.
Learn more about Radial fulfillment centers.