The clean warehouse: a key to ecommerce success
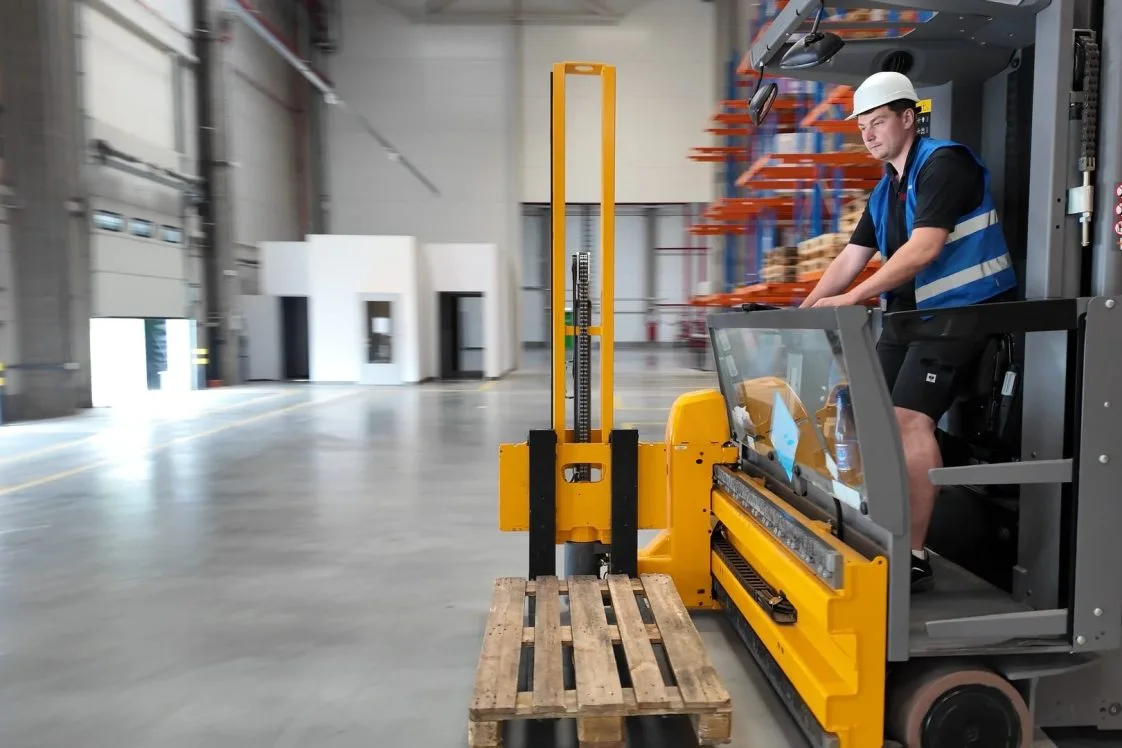
As e-commerce continues to boom, the behind-the-scenes operations of fulfillment warehouses play a crucial role in delivering customer satisfaction. One often overlooked aspect is the cleanliness of these facilities. Here’s why maintaining a clean warehouse environment is essential:
1. Customer centric approach: clean warehouse ensure products remain in pristine condition before shipping. This attention to detail shows respect for customers and their purchases, enhancing the unboxing experience and brand perception.
2. Operational efficiency: a well-organized, clutter-free space improves workflow, reduces errors, and boosts productivity. Workers can locate items faster and move more efficiently in a tidy environment.
3. Employee well-being: clean workspaces promote employee health, safety, and morale. This leads to higher job satisfaction, lower turnover, and ultimately better service for customers.
4. Quality control: a clean facility makes it easier to spot defects or damages, ensuring only top-quality products reach customers.
5. Compliance and safety: regular cleaning helps maintain compliance with health and safety regulations, reducing risks and potential liabilities.
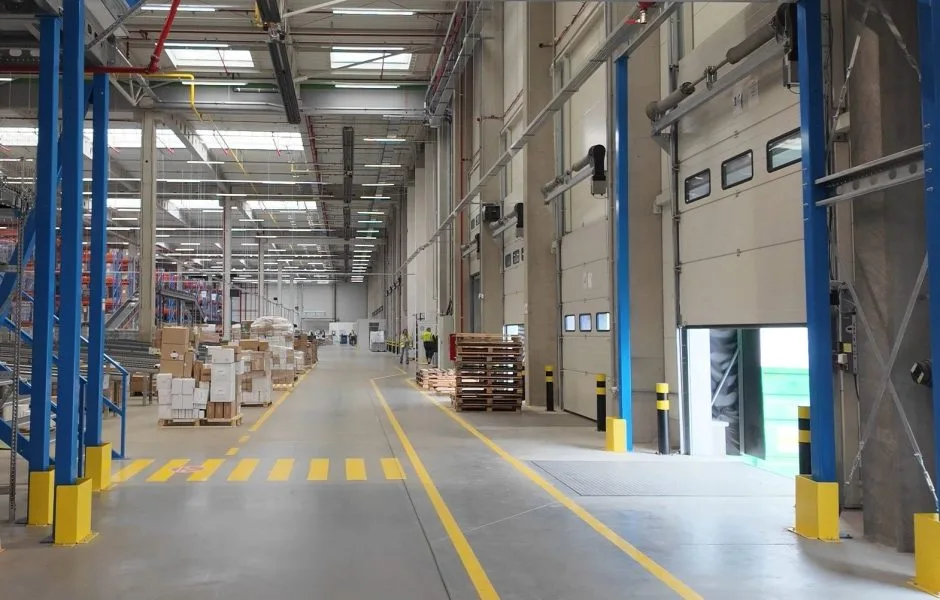
Radial fulfillment center in Warsaw, Poland: A clean warehouse is an essential component of fulfillment services.
Case example: Radial Poland
The Radial Poland team implemented strict cleanliness protocols at all operational stages. The facility is known for its organized layout, ensuring easy access and flow of goods while keeping the working environment free from unnecessary clutter.
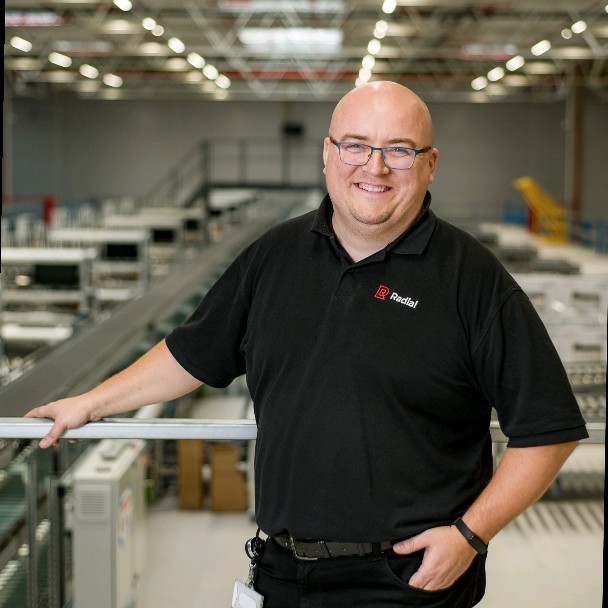
“I’m proud to say that cleanliness and tidiness are a priority for every employee here. Thanks to the commitment of our team and the implementation of the 5S lean management system, we maintain the highest standards in this area. Our customers frequently express their appreciation for the organization and cleanliness of our facility, which reflects our dedication to operational excellence.” — Ireneusz Bińkowski, Operations Manager, Radial Poland
Lean management – 5S
Radial Warsaw has implemented the 5S system: Sort, Set in order, Shine, Standardize, Sustain. By sorting materials, organizing tools, cleaning daily, establishing standards, and maintaining these practices, we ensure a clean and efficient work environment. The 5S checklist is reviewed daily to ensure that all employees consistently maintain the highest standards of tidiness and organization.
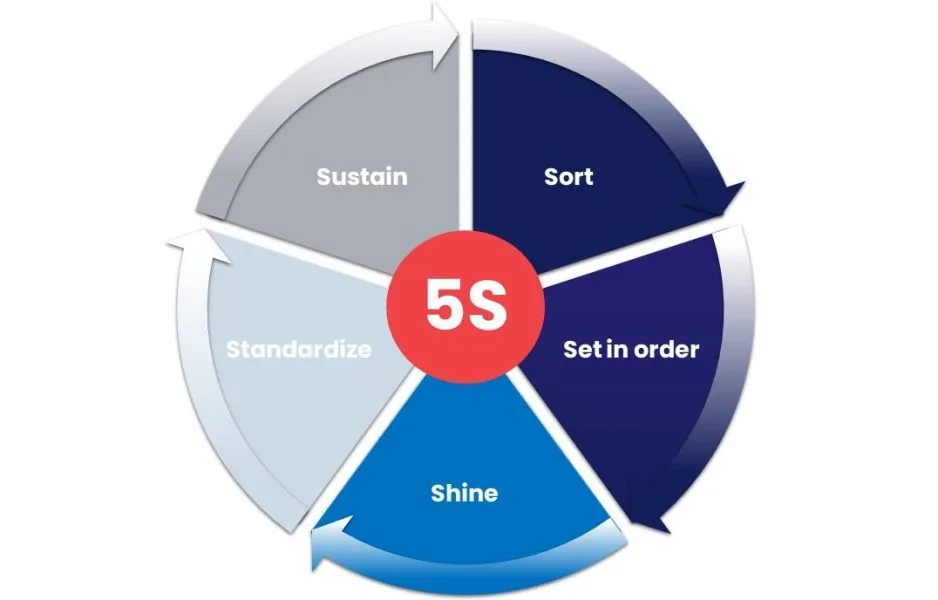
Regular cleaning schedules
In the warehouse, cleanliness is an everyday responsibility. Each employee cleans their workstation at the end of their shift, ensuring the next person has a clean and ready-to-use space. There are designated Cleaning Zones with specific areas for cleaning equipment and supplies.
A dedicated cleaning team ensures that the office spaces and restrooms are cleaned daily, windows twice a year, and the warehouse floor is washed monthly.
Waste segregation practices
Waste segregation is a core element of this facility’s operations. Designated bins for different types of waste: plastic, paper, hazardous materials, are placed strategically throughout the warehouse. This ensures that materials like cardboard, plastic, and metal are recycled appropriately, while hazardous materials, such as chemicals, are disposed of safely according to environmental regulations.
By focusing on cleanliness and responsible waste segregation, Riadal warehouse in Poland exemplifies how high standards can improve operational efficiency and environmental sustainability while ensuring a safe workplace.
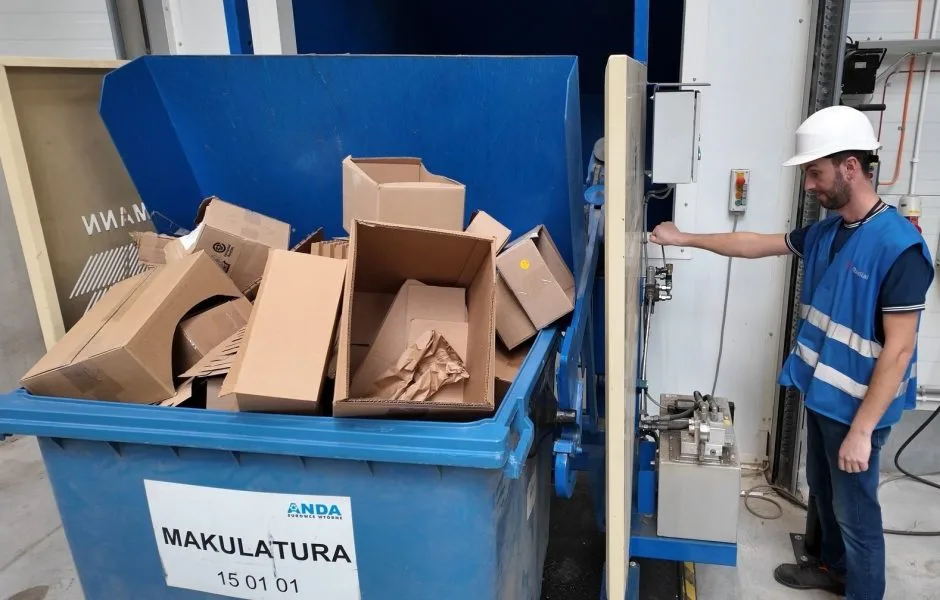
Organized paper segregation system at Radial Poland.
Audits and training
Radial’s team keeps documentation and cleaning logs to track the day-to-day execution and ensure adherence to cleaning protocols.
Regular audits are conducted to ensure compliance with local waste management regulations and internal cleanliness standards. Additionally, employees receive regular training to remain updated on best practices for maintaining cleanliness and managing waste efficiently.
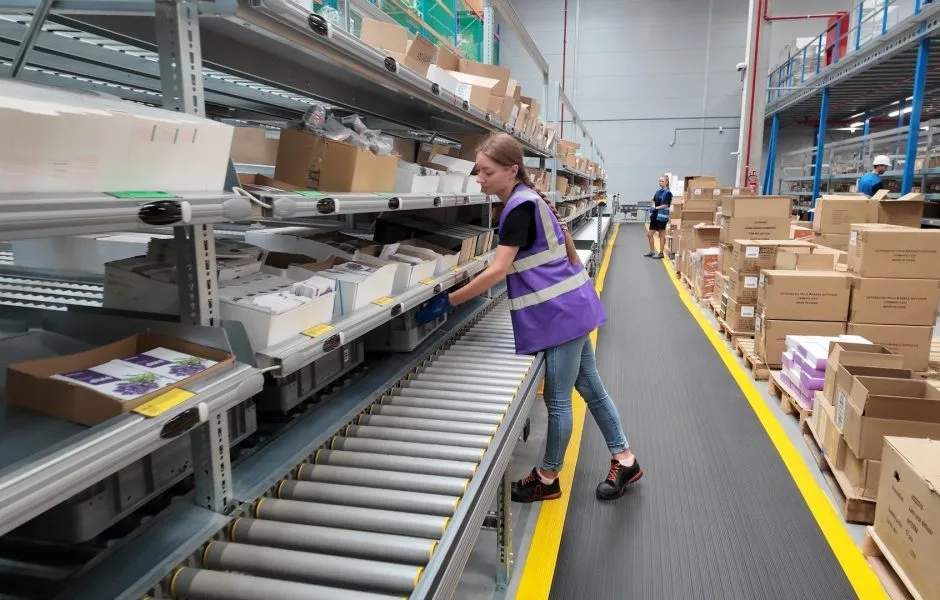
A clean and organized warehouse at Radial Poland ensures efficient operations and safety.
Clean warehouse – general processes
There are standard processes in ecommerce fulfillment to maintain and monitor the cleanliness of warehouses. These processes are crucial for ensuring a safe, efficient, and compliant work environment. Here are some common practices:
- Regular cleaning schedules:
- Daily cleaning of high-traffic areas
- Weekly deep cleaning of workstations and equipment
- Monthly or quarterly cleaning of less-frequented areas
- Cleanliness audits:
- Regular inspections using standardized checklists
- Third-party audits for unbiased assessments
- Waste management:
- Proper sorting and disposal of different types of waste
- Recycling programs for cardboard, plastics, and other materials
- Pest control:
- Regular inspections and treatments
- Preventive measures like sealing entry points
- Air quality management:
- Regular HVAC system maintenance
- Dust control measures
- Employee training:
- Training on cleanliness standards and procedures
- Encouraging a “clean as you go” mentality
- Designated cleaning zones:
- Specific areas for cleaning equipment and supplies
- Clearly marked sanitation stations
- Hygiene protocols:
- Hand washing stations and sanitizers throughout the facility
- PPE requirements in specific areas
- Spill response procedures:
- Quick response protocols for spills
- Proper cleaning and disposal of hazardous materials
- Documentation:
- Maintaining cleaning logs
- Recording and addressing cleanliness issues
- Technology integration:
- Using IoT sensors to monitor air quality or detect spills
- Software for scheduling and tracking cleaning