What is the difference between a fulfillment center and a warehouse?
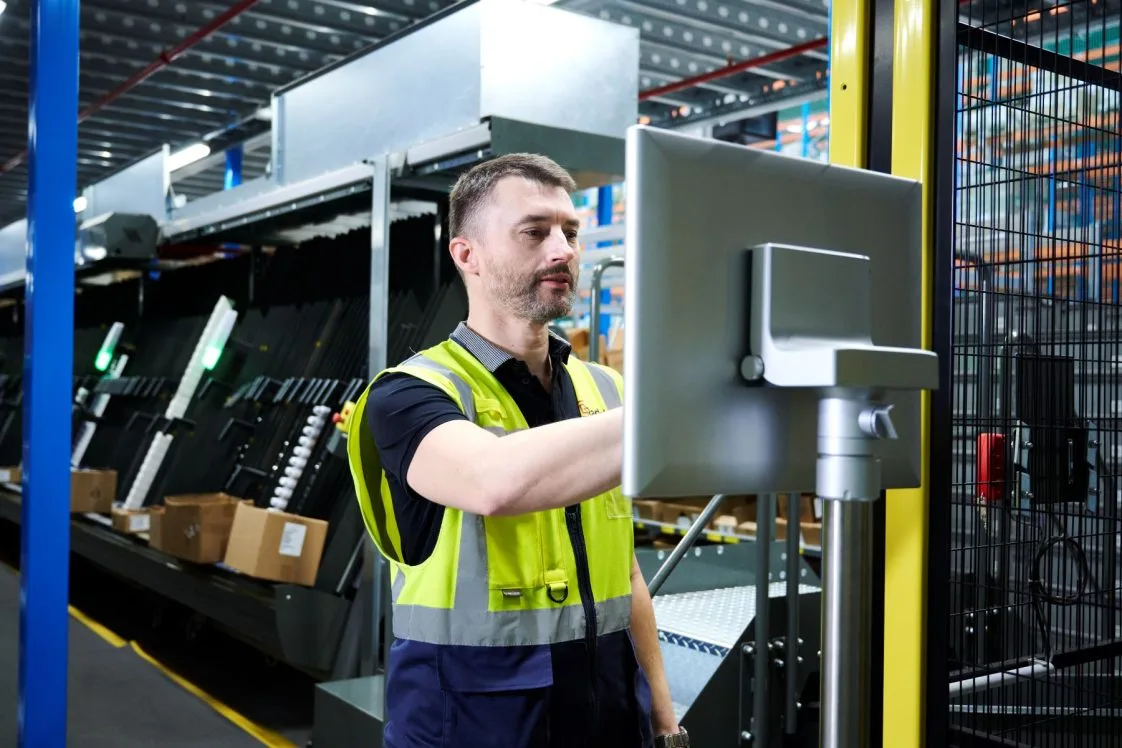
Managing order fulfillment efficiently is crucial for businesses across various industries. As demand grows, handling logistics in-house can become overwhelming. This is where both a warehouse and a fulfillment center come into play, but they serve distinct purposes. While often confused, understanding the difference between them is key to optimizing your supply chain.
What is a fulfillment center?
A fulfillment center is a specialized facility where third-party logistics (3PL) providers manage the entire order fulfillment process for businesses. While storage is a component, it’s just one piece of the puzzle. Fulfillment centers handle everything from receiving and storing inventory to picking, packing, and shipping orders directly to customers. They also manage returns, handle customer service inquiries related to shipping, and often offer value-added services like kitting and labeling. Fulfillment centers are designed for speed and efficiency, focusing on getting orders out the door quickly and accurately. They prioritize speed, accuracy, and customer satisfaction in order processing.
What is a warehouse?
A warehouse primarily focuses on the storage of goods. Think of it as a large storage facility where inventory is kept until needed. Warehouses are important for holding large quantities of products, often for extended periods. They provide space for businesses to stockpile inventory, manage excess stock, and prepare for future demand. While some warehouses may handle basic shipping and receiving, their core function is storage. Orders are typically processed in bulk or larger quantities for distribution to retailers or other facilities. The picking, packing, and shipping of individual customer orders may not be as optimized or streamlined as in a dedicated fulfillment center.
The key differences between a warehouse and a fulfillment center
Warehouse | Fulfillment center |
Storage of goods | Order fulfillment (receiving, picking, packing, shipping) |
Holding inventory | Processing and shipping orders |
Slower, focused on long-term storage | Fast, focused on rapid order processing |
Basic storage, potentially some shipping/receiving | Comprehensive order fulfillment, including returns and value-added services |
Businesses needing large-scale storage | Businesses needing efficient order processing, especially e-commerce companies |
Basic inventory tracking | Advanced, real-time inventory management |
May have basic systems | Sophisticated warehouse management systems (WMS) and integration with sales platforms |
Less emphasis on rapid flow | Optimized for smooth and rapid product flow using technology like automated conveyor belts, robotics, and real-time data analysis |
Primarily storage-focused | Complex operations including picking, packing, shipping, and real-time inventory updates via integrated software |
Long-term storage | Fast and efficient order fulfillment |
How a fulfillment center works?
The fulfillment process follows a structured workflow to ensure efficiency. It begins with receiving inventory, where products are checked for accuracy and stored in designated locations within the facility. When an order is placed, the system automatically retrieves the necessary information, and staff or automated systems pick the required items from inventory. These items are then packed securely, often with branding and protective materials, before being labeled for shipping. Finally, the fulfillment center coordinates with shipping carriers to ensure prompt delivery. Throughout the process, real-time tracking and quality control measures help maintain accuracy and customer satisfaction.
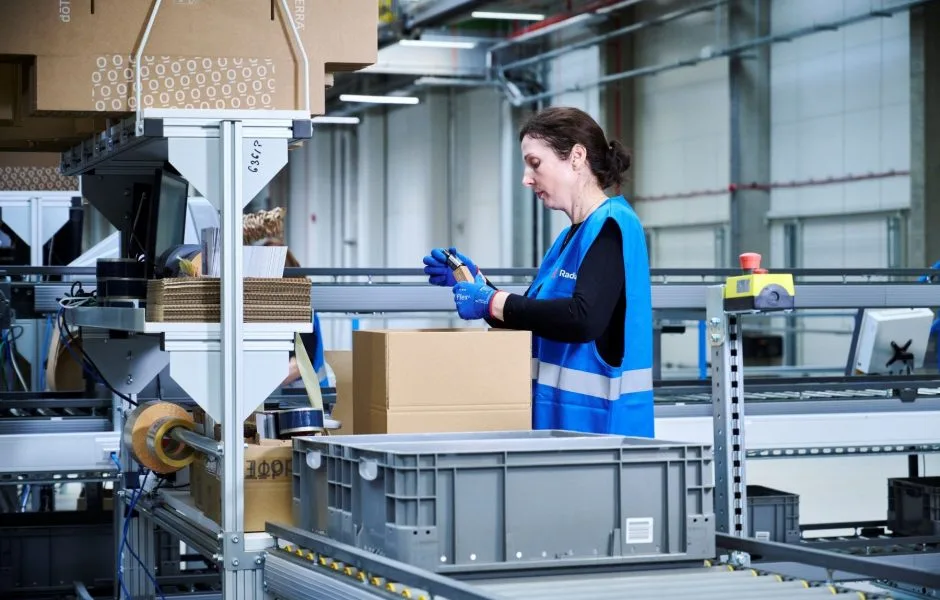
A Radial team member carefully packs items to fulfill a customer order.
Types of fulillment centers
Fulfillment centers come in various types, each tailored to specific business needs and product characteristics. Understanding these different types can help businesses choose the best fit for their operations.
- Single-vendor fulfillment centers: dedicated to a single business, providing customized storage and logistics solutions. This offers greater control and flexibility but can be more expensive. A large e-commerce company with unique product handling requirements might opt for this type.
- Multi-vendor fulfillment centers: also known as shared warehousing or co-warehousing, these facilities serve multiple businesses within a shared space. This model optimizes costs and efficiency by pooling resources and sharing overhead. Smaller businesses or startups with fluctuating inventory levels often find this option more affordable and scalable.
- Specialized fulfillment centers: focused on specific industries or product types (food, pharmaceuticals,chemicals or batteries) ensuring compliance with industry regulations and handling requirements.
- On-demand fulfillment centers: offer flexible, pay-as-you-go services, often used by businesses with unpredictable sales volumes or seasonal products. They provide scalability without the commitment of long-term contracts.
- Dropshipping fulfillment centers: the fulfillment center not only stores the products but also directly ships them to the end customer on behalf of the retailer. The retailer never physically handles the inventory.
- Direct-to-consumer (D2C) fulfillment centers: designed specifically for businesses selling directly to consumers, emphasizing fast shipping and personalized customer experiences. They often integrate with e-commerce platforms for seamless order processing.
- Retail fulfillment centers: these cater to businesses that sell through retail channels, often requiring different labeling and packaging than D2C orders. They may also handle store replenishment.
- Tailored fulfillment centers: emphasize the customization and bespoke solutions. While many fulfillment centers offer some level of customization, “tailored” centers go further, working closely with businesses to design and implement solutions that perfectly match their unique needs, even if those needs are complex or unusual.
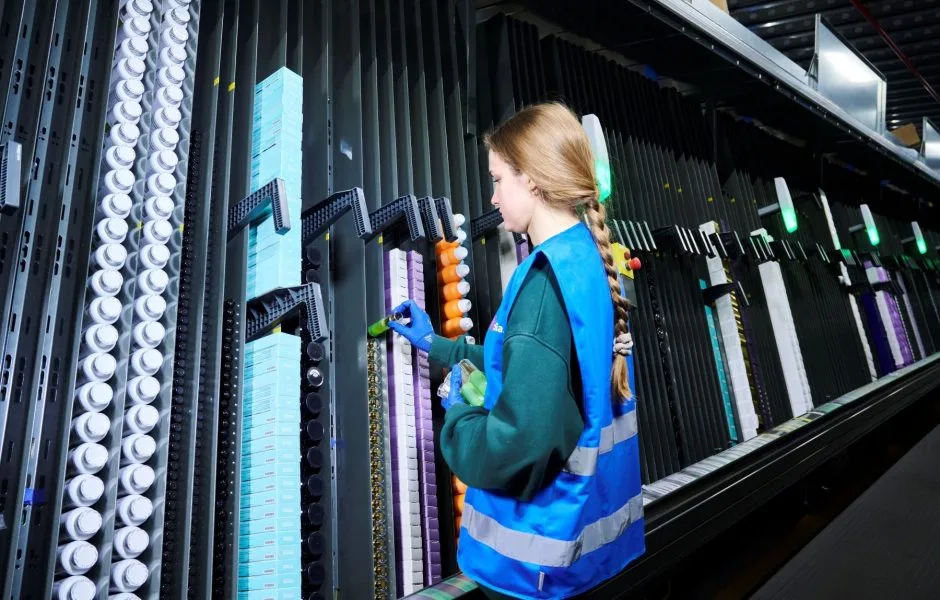
The A-frame system, designed to meet the high standards of a key Radial client, provides gentle and precise handling for cosmetics and lifestyle products, including delicate items like small bottles of essential oils.
Benefits of partnering with a fulfillment center
Partnering with a fulfillment center offers significant advantages for businesses of all sizes, from startups to large enterprises:
Access to Expertise and Technology: Fulfillment centers offer access to specialized expertise in logistics, warehousing, and shipping, as well as advanced technologies like warehouse management systems (WMS) and order tracking software. This can be particularly beneficial for businesses that may not have the resources to invest in these areas themselves.
Reduced Overhead Costs: By outsourcing warehousing and fulfillment, businesses can avoid or minimize investments in warehouse space, equipment, and staffing. This frees up capital for other crucial areas of the business, such as product development, marketing, or expansion.
Expanded Market Reach: Fulfillment centers can strategically position inventory closer to customers, enabling faster and more cost-effective shipping, even across wider geographic areas. This allows businesses to reach new markets and compete more effectively, regardless of their size.
Improved Efficiency and Scalability: Fulfillment centers specialize in streamlined processes, advanced technology, and efficient workflows, leading to faster order processing and improved delivery times. They also provide the scalability to handle fluctuations in demand, whether it’s a seasonal spike or rapid business growth, without overwhelming internal resources. For example, a business experiencing a surge in orders can rely on the fulfillment center to manage inventory levels and ensure timely customer deliveries.
Focus on Core Business Activities: Outsourcing fulfillment allows businesses to focus on their core competencies. Whether it’s product innovation, customer relationship management, or strategic planning, outsourcing logistics frees up valuable time and resources, allowing companies to concentrate on what they do best.
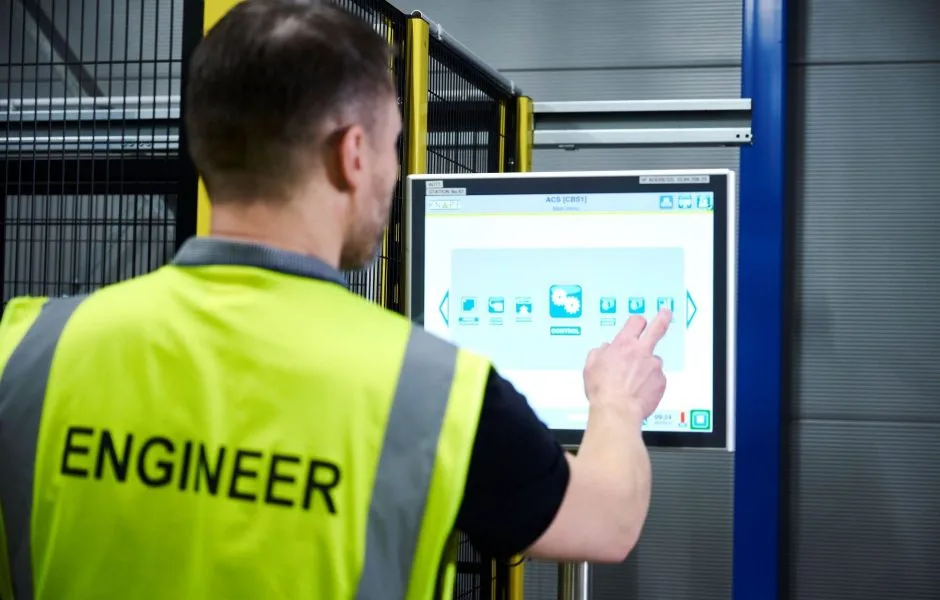
Radial leverages warehouse control software to optimize its warehouse operations. The software intelligently controls and coordinates goods flow within the automated system, resulting in efficient and error-free processing.
Wide range of businesses across diverse industries
Fulfillment centers offer valuable support to a wide range of businesses across diverse industries. Their flexible and efficient services cater to specific needs, enabling companies to meet industry demands and support growth. Here are some examples:
- Beauty brands: Shipping skincare products, cosmetics, and other personal care items, often requiring specialized packaging and handling.
- Healthcare product brands: Managing vitamins, supplements, health foods, and other wellness products, sometimes requiring specific storage conditions or regulatory compliance.
- Sports brands: Distributing equipment, apparel, and accessories, often dealing with bulky or irregularly shaped items.
- Fashion and apparel brands: Managing clothing, shoes, and accessories, often requiring specialized storage, garment handling, and efficient returns processing.
- Direct sales companies: Managing and shipping products sold through independent distributors or representatives, often requiring specialized kitting, packaging, and distribution to multiple locations.
- E-commerce businesses: Handling a wide variety of products, from electronics to apparel to home goods, focusing on fast and accurate order fulfillment.
- Publishing companies: Distributing books, magazines, and other printed materials.
- Manufacturing companies: Storing and shipping raw materials, components, or finished goods.
For businesses looking to optimize operations and improve efficiency, utilizing a fulfillment center is a strategic move. While a warehouse provides essential storage, a fulfillment center empowers businesses to scale, improve delivery times, and focus on their core competencies. No matter the industry or product type, fulfillment centers provide the infrastructure, expertise, and technology necessary to streamline logistics and enable businesses to scale effectively.