Driving continuous improvement: the 5S
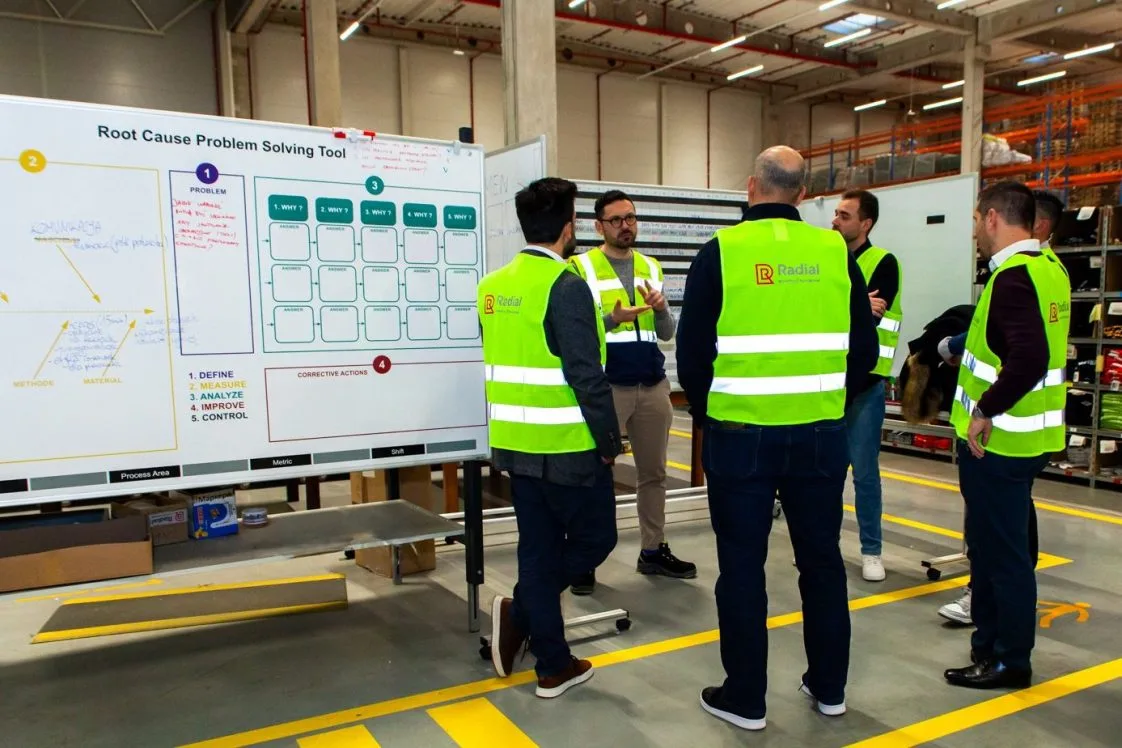
Expert Contributor by Karol Wojciechowski, Operations Manager at Radial Europe
The 5S at Radial Poland
Introducing the 5S methodology has been one of the most impactful initiatives I’ve led at Radial Poland. As responsible for its rollout, I’ve experienced how this methodology can transform a workplace. The team in Poland was the first to introduce it, followed by the teams in other sites.
Our goal is to expand it across all our European units. In Radial Poland, the 5S approach was adapted alongside our transition to automation in December 2022. Preparations began six months earlier to ensure a smooth shift from manual to automated processes. Today, the 5S methodology is a key part of our operations.
What is the 5S methodology?
The 5S is a well-established system for workplace organisation and efficiency, based on five Japanese principles:
- Sort
- Set
- Shine
- Standardize
- Sustain
These principles aim to create a clean, well-organized, and efficient workspace that minimizes waste, enhances safety, and boosts productivity. Originally developed in Japan as part of Lean Manufacturing, 5S has become a globally recognized tool for improving operations in warehouses and production environments.
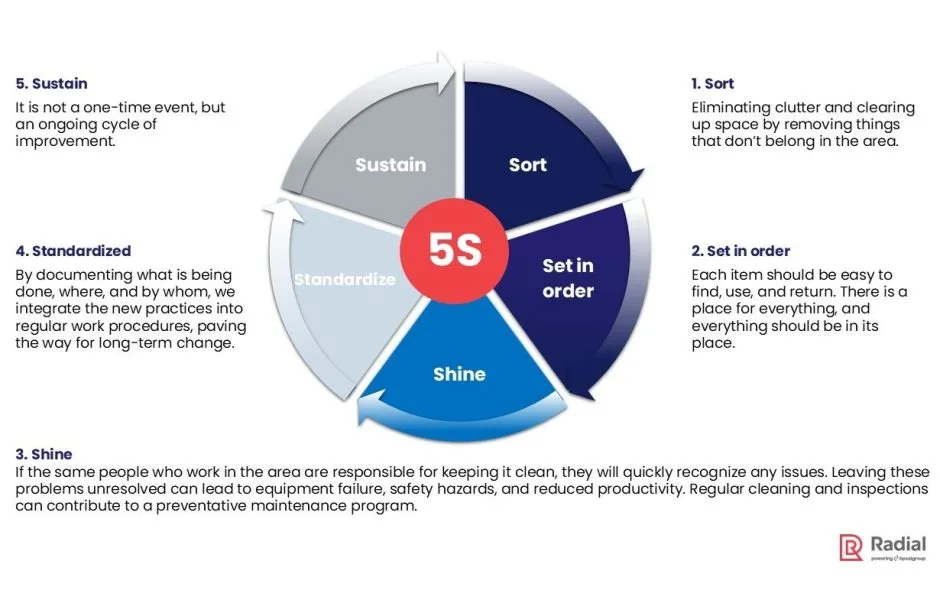
Why do we use it?
The primary goal of adopting the 5S methodology is to enhance safety for goods and, most importantly, for people.
By improving physical working conditions and fostering a safety-focused culture, 5S actively engages employees in maintaining cleanliness and shared responsibility for workplace safety.
This consistent adherence to organizational standards shifts mindsets, raising awareness of potential hazards and promoting preventive measures to address them effectively. The importance of 5S is especially pronounced in automated warehouses, where maintaining order and safety is critical to operational success.
Challenges in introducing 5S
Applying 5S at Radial Poland required a comprehensive approach and a shift in mindset across the organization.
The challenge was to make employees understand that 5S is not a one-time initiative but a continuous process dependent on self-discipline and adherence to established standards. Proper training was essential. Without a clear understanding of 5S principles and their benefits, employees might not have adopted the methodology in full, impacting its success.
To address this, we conducted training sessions at all operational levels and engaged employees in workshops to highlight common wastes (Muda) in processes.
By analyzing existing workflows through this lens, staff began to identify areas for improvement. The focus shifted from changing old habits to adopting a mindset of continuous enhancement.
5S is more than a set of steps. It is a tool that supports waste elimination and fosters ongoing improvements in the way we think and act.
THE MAIN BENEFITS OF ADOPTING THE 5S METHODOLOGY
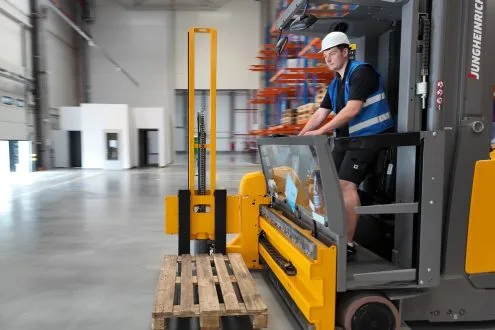
- Improved workplace ergonomics
- Increased safety standards
- Elimination of unnecessary movements (e.g. elimination of waste)
- Increased quality of work
- Stabilization of work pace by reducing distractions
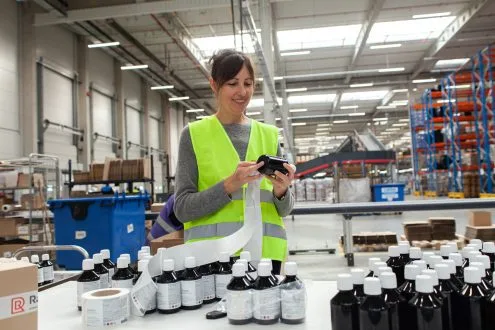
- Improved workflow
- Accessibility and visibility of all tools
- Consistent order and systematics
- Safety at the workplace
- Increased job satisfaction
- High organizational culture
- Adaptation of the workplace to the activities performed
- Stability of processes
- Ergonomics of the workplace
- Friendly environment
- Reduction of the consumption of tools and materials
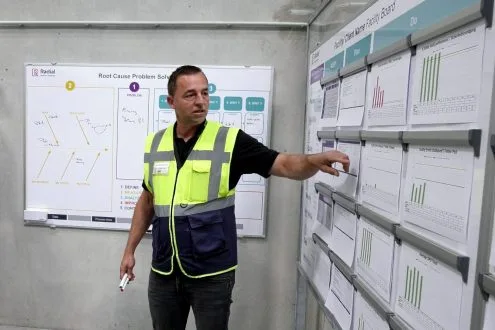
EFFECTIVENESS
- Standardization based on experience
- Arrangement of necessary tools at hand
CONTINUOUS IMPROVEMENT
- Facilitate communication with colleagues
- Increasing knowledge and commitment
Examples of 5S in practice
Shine – keeping the packaging area clean
In a dynamic warehouse environment, particularly in the packing areas, dust, tape, and packaging residues accumulate on workstations, compromising the quality of packaging and potentially affecting lead times.
Actions:
- Implementing daily cleaning routines, with a focus on the packing areas, ensuring cleanliness and tidiness.
- Equipping each workstation with cleaning supplies and necessary tools.
- Establishing the ‘end-of-work cleanliness standard’, making each employee responsible for cleaning their station at the end of their shift.
- Introducing regular cleaning checks and audits to maintain high cleanliness standards.
Results: These measures reduced product damage during packaging, enhanced customer service through cleaner packaging, increased employee comfort, and boosted productivity.
Standardize – Introduce uniform operating procedures
In a multi-customer warehouse, variability in order processing due to the absence of standardized procedures resulted in errors, inconsistent packaging, and long lead times.
Actions:
- Creating detailed procedures for all stages of the process, including goods receipt, quality control, product scanning, packaging, and dispatch.
- Introducing homogeneous forms and documents for each stage, enabling easier tracking of order progress.
- Providing operational instructions and training to ensure adherence to the new standards.
Results: Standardizing processes reduced errors and delays, improved operational efficiency, and ensured better quality control at each stage of order fulfillment.
Sustain – Maintenance of 5S Standards by the Team
After adopting 5S in an automated warehouse, there were challenges in maintaining standards, with unnecessary items accumulating and processes becoming less efficient.
Actions:
- Designating 5S leaders within the team to oversee compliance and maintain order in the warehouse.
- Organizing regular 5S audits, taking place weekly or monthly, to assess cleanliness, tidiness, space organisation, and adherence to procedures.
- Encouraging employees to continuously improve through reminder sessions on 5S principles and setting goals for future improvements.
Results: These efforts ensured long-term maintenance of 5S standards, preserving high operational efficiency in the warehouse.
Determining the most efficient warehouse layout
An efficient warehouse layout is essential for minimizing picking time and increasing accuracy. The key lies in analyzing the flow of goods, selecting the appropriate storage methods, leveraging modern technology, and continuously improving processes.
Warehouse strategies must be tailored to the specific characteristics of the products and the space available. No one-size-fits-all approach exists.
To maximize picking efficiency, various factors must be considered, acting like a set of interconnected elements. A crucial component is the Warehouse Management System (WMS). At Radial, we use Manhattan Active, continuously enhanced with new functionalities.
Testing and ongoing process improvements are central to refining our layout. By analyzing data such as picking times, order accuracy, and error rates, we identify areas for improvement and adjust our strategies accordingly. This data-driven approach helps ensure that our warehouse layout remains optimized for efficiency and accuracy.
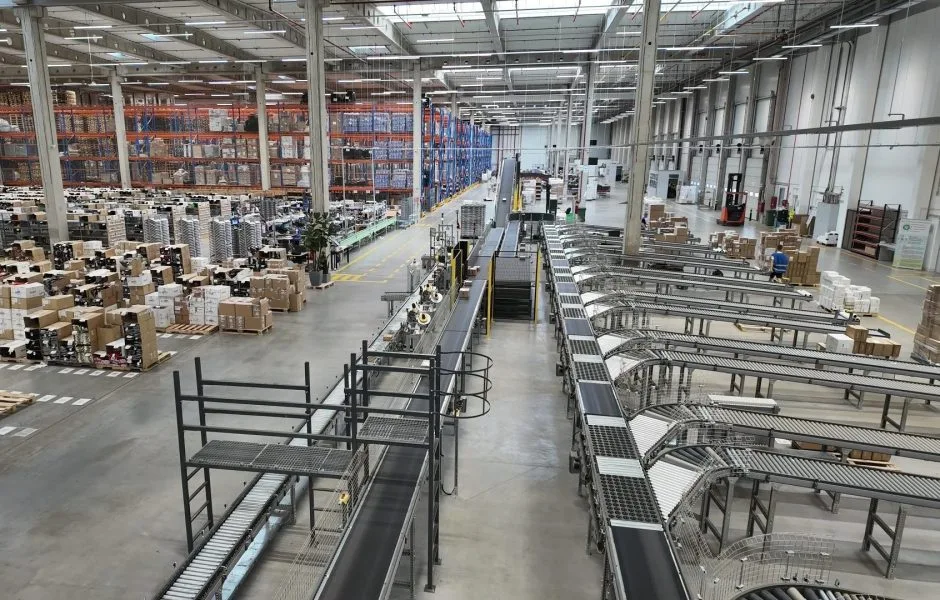
Results and measurement of 5S effectiveness
The tangible benefits of applying 5S include improved warehouse organization, elimination of unnecessary items, and more precise labeling of storage locations. These improvements lead to quicker product retrieval and greater operational efficiency in loading, unloading, and picking.
Key success metrics include the time required to complete warehouse operations, such as the time to find goods and pick an order. We also track the number of errors in goods location, measured in items and orders processed per employee per shift. These metrics provide insight into the impact of 5S on warehouse performance and help guide further improvements.
Sustaining 5S and supporting continuous improvement
Management commitment is crucial for sustaining 5S and fostering a culture of continuous improvement. Introducing 5S goes beyond altering the physical layout; it requires changing the way the entire team thinks and works.
Leaders play a key role in ensuring the success of 5S. They define its goals, align it with the company’s strategy, and prioritize its integration into daily operations. Without this commitment, employees may see 5S as a temporary initiative, not a lasting cultural shift. This commitment is essential for its long-term effectiveness.
Customer experience
In fulfillment centers, speed, accuracy, and packaging quality are key factors in customer satisfaction. By applying the 5S, we have improved process efficiency, reduced errors, and enhanced accuracy in order fulfillment. These improvements directly contribute to a better customer experience.
Our goal is to ensure that customers are satisfied with the services we provide, helping to grow their businesses.
Recommendation for other companies
Introducing 5S in warehouse logistics is a complex but highly beneficial process. It requires team involvement, careful planning, and overcoming challenges such as resistance to change, the need for training, space reorganization, and initial investments. However, with strong management support, 5S can significantly boost operational efficiency, improve work quality, and enhance safety.
Moreover, the 5S promotes sustainability by optimizing space and managing resources more efficiently. A tidy and well-organized warehouse reduces the consumption of energy, paper, packaging, and other resources, positively impacting the environment. By consistently applying 5S principles, companies can achieve greater efficiency, reduce costs, improve the working atmosphere, and ultimately enhance business performance. This makes 5S a method worth considering for any company in the industry.
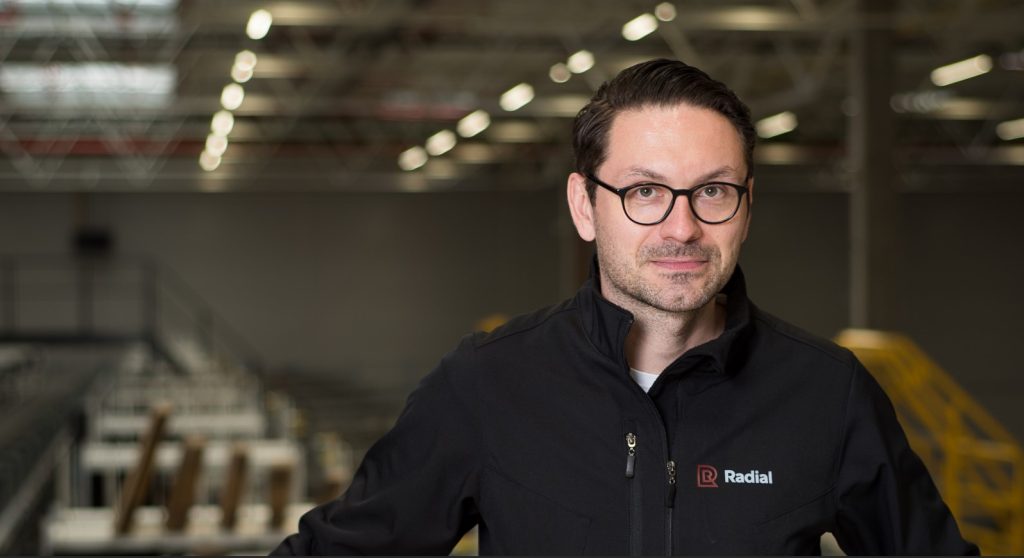
About the author
Karol Wojciechowski, Operations Manager at Radial Europe, is an experienced Warehouse and Logistics Manager with a strong focus on E-commerce and Lean Green Belt® methodologies. Karol is highly organized, process-driven, and detail-oriented, with a proven ability to deliver operational solutions to complex logistical problems. He holds postgraduate degrees in Logistics Management and Digital Supply Chain from Kozminski University and WSB University.